Koyo Technical Information
a. Limiting speed of bearings
The rotating speed of a bearing is normally affected by friction heat generated in the bearing. If the heat exceeds a certain amount, seizure or other failures may occur in a bearing, thus causing rotation to be discontinued.
Limiting speed of bearing refers to the rotating speed at which the bearing can be rotated continuously without excessive increase in temperature. And in case of a sealed bearing with contact type seal, the rotating speed is limited by two more factors; those are running speed of seal contact surface and heat-resistance characteristics of packed grease.
Limiting speed of bearing varies depending on the bearing type, dimensions, accuracy, lubrication method, the properties and amount of lubricant, the type and material of cage, and loading conditions.
The lubrication based limiting speed for each bearing is listed in the bearing specification tables (grease or oil bath). When bearing rotating speed is close to or higher than the limiting speed specified in this catalogue, consult Koyo. The limiting speed specified in the bearing specification tables applies to operation under normal loading conditions (C/P≥13, Fa/Fr≤ approx. 0.25).
C | : basic dynamic load rating | N | |
Fr | : dynamic equivalent load | N | |
Fr | : radial load | N | |
Fa | : axial load | N |
b. Correction of limiting speed
When C/P is greater than 13 and/or Fa/Fr is greater than 0.25, adjust the limiting speed by means of the equation shown below. na=f1f2
n
Where:
na: | corrected limiting speed | min-1 |
f1: | correction factor determined from the load magnitude, | (Fig.5-1) |
f2: | correction determined from combined load | (Fig.5-2) |
n: | limiting speed under normal load condition (values in the bearing specification table) |
min-1 |
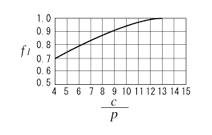

c. Consideration for high speed
Examine the following points when using a bearing near or beyond its limiting speed.
For further information on high speed rotation, consult Koyo.
1) Use of high precision bearings
2) Study of proper internal clearance (Reduction in internal clearance caused by temperature increase should be considered.)
3) Selection of proper cage type and materials (For high speed, copper alloy or phenolic resin machined cages are suitable.)
4) Selection of proper lubrication (Suitable lubrication for high speed should be selected forced oil lubrication, oil jet lubrication, oil mist lubrication and oil/air lubrication, etc.)
d. Friction coefficient of bearings
The friction moment of rolling bearings can be obtained from their bearing bore diameter, using the following equation:
M=µPd/2
Where:
M: | friction moment | mN · m |
µ: | friction coefficient | (Table 4-1) |
P: | load on the bearing | N |
d: | nominal bore diameter | mm |
Type of bearing | Friction coefficient µ |
---|---|
Deep groove ball bearing | 0.0010 to 0.0015 |
Angular contact ball bearing | 0.0012 to 0.0020 |
Self-aligning ball bearing | 0.0008 to 0.0012 |
Cylindrical roller bearing | 0.0008 to 0.0012 |
Full complement type needle roller bearing | 0.0025 to 0.0035 |
Needle roller and cage assembly | 0.0020 to 0.0030 |
Tapered roller bearing | 0.0017 to 0.0025 |
Spherical roller bearing | 0.0020 to 0.0025 |
Thrust ball bearing | 0.0010 to 0.0015 |
Spherical thrust roller bearing | 0.0020 to 0.0025 |
<Ref> Plain bearing | 0.01 to 0.02 |
d. Passing vibration frequency
As the rolling elements pass the loading position, even under normal operation, a small vibration can occur due to elastic deformation of components (inner ring/outer ring/ball).
This is called passing vibration of rolling elements. A failure on the contact surface of the components may generate vibration as rolling elements pass the failure position. The frequency of such vibration differs depending on where the failure lies; therefore, it is possible to learn whether the bearing has a failure, and if so, where, simply by measuring the vibration frequency of the system and comparing it with calculated values.
For calculation of such vibration frequency, use the Menu entitled Passing Vibration Frequency.